Are Composite Struts Appropriate for the Extrication Environment?
If you are considering pultruded Fiberglass Reinforced Polymer (FRP) composite struts, please consider the following. We want to be sure you are familiar with not only the advantages of such materials, but also the not so desirable characteristics. With this knowledge you can make an informed decision on your strut material selection. We encourage you to select the safest and most sensible material for your given application. There are several environmental, handling, storage, and application concerns you should be fully aware of that may not only increase the usable life of your composite strut, but provide you with critical life safety information that could keep you out of a disastrous situation. In a University of Missouri article, Antonio Nanni states that “using FRP in the wrong application is like hammering a square peg into a round hole.”
There’s a good chance that your interest in composite struts is due to some of the marketing hype touting composite struts as “stronger than steel”, non-conductive, lightweight, etc. There is some truth to the above, but you need the whole truth to make an educated selection.
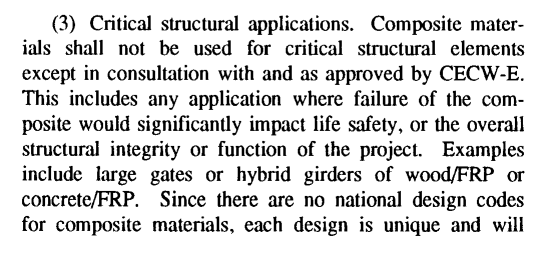
Taken from: https://apps.dtic.mil/dtic/tr/fulltext/u2/a403282.pdf
Regarding strength of pultruded FRP composites relative to steel, composite engineers have suggested that the composite cross-sectional area should be about three times the cross-sectional area of a similar steel structure to equal the strength. In other words to match the strength of a 2” square steel tube with an 1/8” thick wall, you would need a 2” square composite tube with about a 3/8” thick wall. Unit for unit steel is stronger than most FRP pultruded composites.
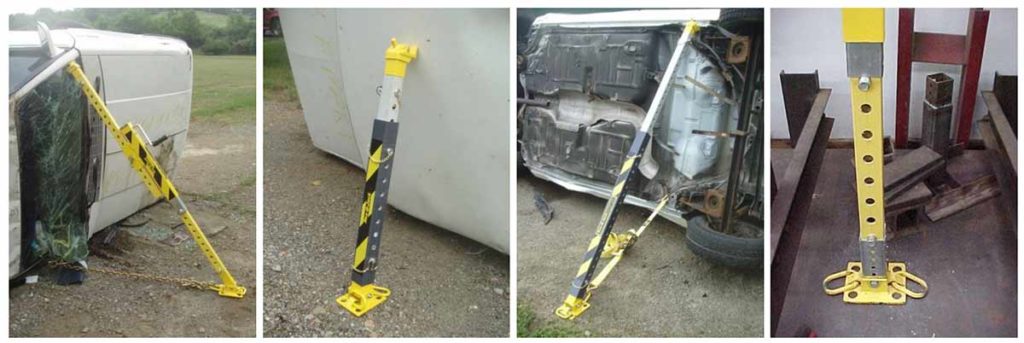
Pictured above are FRP (fiberglass reinforced polymer) composite prototypes from Res-Q-Jack. Due to poor testing results Res-Q-Jack concluded that this material has no place in the extrication environment.
Pultruded FRP composites are poor performers when it comes to cross-wise impact loading. These are materials that you do not want to drop on objects or drop objects on. In a simple test, a 6 lb. round weight was dropped from waist height onto a 2.5” square piece of FRP pultruded composite tubing with a ¼” thick wall. The material was destroyed by the impact. The same test performed on galvanized steel tubing 2.25” square with an 1/8” thick wall produced little effect. Another problem in the world of composites is pinned joints. Great care must be taken in fastener selection and joint design due to the low hole bearing stress capacity. Pins and thus holes must be of a large diameter to spread the bearing load over a greater wall surface area. Steel on the other hand can withstand a much greater fastener bearing load. A 3/8” diameter pin in double shear will pulverize the side wall of 2” square FRP pultruded composite tubing with a ¼” thick wall at about 6,000 lbs. 2” square steel tubing with an 1/8” wall will handle about twice the load without hole bearing damage.
If your application environment involves abrasion, you may want to avoid composites. Pultruded FRP composite tubes are very susceptible to abrasive wear. Sliding contact between this material and any abrasive material like asphalt, concrete, or other materials will damage the tubing surface. The scratches or gouges that occur remove the protective veil that aids in UV resistance and fiber protection. Wear can be significant enough that tubing strength is questionable. Wear believed to be caused by vibratory contact between strut mounts and composite struts during transportation has been reported. The observed wear was a horizontal recess across the face of a tube wall. The depth of the recess was about 1/16”. That’s 25% of the wall thickness if using ¼” wall material. Protective sleeves similar to those used with composite SCBA cylinders may be a good solution for storage related wear.
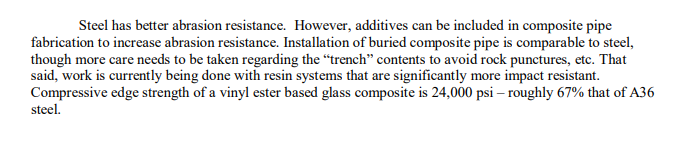
Taken from: http://citeseerx.ist.psu.edu/viewdoc/download?doi=10.1.1.165.1163&rep=rep1&type=pdf
Moisture can cause problems with composites as well. Liquids such as water, oil, fuel and bodily fluids are typically prevented from entering a pultruded FRP composite material when all exposed surfaces are sealed and damage free. However, composite tubes used for stabilization struts have cut exposed ends, cross-wise holes drilled through, and if used in an abusive environment like extrication they most likely have abrasive and/or impact damage. These are all paths for moisture from a water source or humid atmosphere to enter the matrix and occupy the voids. Moisture can lead to swelling of the composite material. With close fitting telescopic tube sections this may cause problems with the telescoping ability. Moisture embedded in the strut will affect the dielectric strength by reducing the electrical insulating capacity of the material as well. Depending on alkalinity of the water and fiber type, the moisture may have a corrosive effect on fibers. Moisture in composites can be removed in a drying oven.

Taken from: http://citeseerx.ist.psu.edu/viewdoc/download?doi=10.1.1.165.1163&rep=rep1&type=pdf
FRP composites may contain additives that retard UV related effects. This protective additive should hold up well for some time, although its effectiveness decays over time. However, surface damage removes the protective covering allowing UV radiation to become a problem. “Fiber blooming” is one form of UV damage.
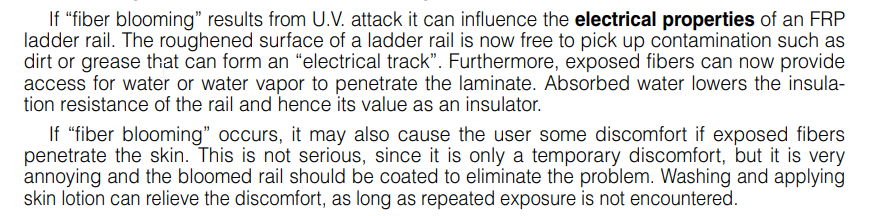
Taken from: https://www.wernerco.com/docs/default-source/literature/gm6070-fg-techmanual.pdf?sfvrsn=dda06ff2_2
High temperatures can be a concern with composites. We are not as concerned with air temperature as we are concerned with asphalt temperature and near surface temperatures where struts may be staged. High temperatures can decrease the strength of composites. According to one manufacturer of FRP tubing, 100°F will reduce the strength by 15%, 125°F will decrease the strength by 30%, and 150°F will decrease strength by 50%. What is the road surface temperature in Phoenix when the air temperature is 120°F? One source indicates that an 86°F air temperature in direct sunlight may produce a 131°F degree road surface.
Regarding the use of FRP pultruded composites as an electrical insulator: Yes, FRP composites are great electrical insulators if the material is clean, dry, and undamaged. As mentioned above, moisture and contamination can significantly reduce the insulating abilities of the material.
Regardless of issues that can adversely affect the insulating capacity, in an electrical hazard situation, it will do little good to have an insulated strut with an uninsulated steel end fitting that the firefighter holds while engaging the vehicle.
Electrical conductivity properties should be a non-issue not only for the reasons stated above, but for the mere reason that it would be ludicrous to knowingly stabilize a charged vehicle. If the rescuer does not know that the vehicle is charged, he or she is in trouble if they are holding an uninsulated strut head in their hands while engaging the vehicle. The material of the strut is irrelevant. One must still consider the challenge of attaching the base restraint to the vehicle. The bottom line is that the dielectric strength of the strut is not a concern.
With the above in mind, it should be no surprise that we do not recommend the use of pultruded FRP composite struts for use in everyday vehicle rescue as the environment is simply too harsh for the material. However, these lightweight struts may be the solution for another specific rescue operation you may encounter. It may be useful to have a set available for that situation where the struts must be carried a great distance to get to the scene such as some wilderness situation.